Boosting Energy Efficiency in Commercial Buildings: Smart HVAC Strategies for Kansas City Businesses
Boosting Energy Efficiency in Commercial Buildings: Smart HVAC Strategies for Kansas City Businesses
In the competitive landscape of Kansas City's commercial sector, energy efficiency isn't just an environmental consideration—it's a critical business strategy. Anderson Mechanical specializes in helping businesses across the metropolitan area optimize their HVAC systems to reduce operational costs, enhance performance, and create more sustainable workplace environments.
The High Cost of Energy Inefficiency
Commercial buildings in areas like Overland Park, Olathe, and Kansas City consume massive amounts of energy, with HVAC systems often accounting for 40-60% of total energy expenditure. For facility managers and business owners, this represents a significant opportunity for cost savings and operational improvement.
Understanding Energy Consumption Challenges
Financial Impact
- Average commercial buildings waste up to 30% of their energy consumption
- Potential annual savings of thousands of dollars through strategic HVAC optimization
- Direct correlation between energy efficiency and bottom-line performance
Environmental Considerations
- Reduced carbon footprint
- Alignment with corporate sustainability goals
- Potential qualification for energy efficiency incentives and tax credits
Smart HVAC Technologies: The Future of Commercial Energy Management
Intelligent Building Automation Systems (BAS)
Advanced building automation systems transform how commercial spaces manage energy consumption:
Real-Time Monitoring Capabilities
- Continuous performance tracking
- Instant identification of inefficiency points
- Predictive maintenance alerts
- Granular energy consumption insights
Adaptive Climate Control
- Zone-based temperature management
- Occupancy-driven temperature adjustments
- Automatic scheduling based on business hours
- Reduction of unnecessary heating and cooling
Advanced Sensor Technologies
Modern sensor technologies provide unprecedented control and efficiency:
Occupancy Sensors
- Automatically adjust HVAC output based on actual room usage
- Eliminate energy waste in unoccupied spaces
- Seamless integration with existing building infrastructure
Sophisticated Temperature Mapping
- Precise temperature control across different building zones
- Compensation for external temperature variations
- Elimination of hot and cold spots
Strategic Implementation Approaches
Comprehensive Energy Audit
Our approach begins with a detailed energy assessment:
- Thorough examination of existing HVAC infrastructure
- Identification of inefficiency points
- Customized optimization recommendations
- Cost-benefit analysis of proposed upgrades
Technology Integration Strategies
Smart Thermostat Implementation
- Programmable learning thermostats
- Cloud-connected climate management
- Advanced scheduling capabilities
- Remote monitoring and control
Variable Refrigerant Flow (VRF) Systems
- Highly efficient multi-zone temperature control
- Significant energy consumption reduction
- Flexible installation options
- Minimal ductwork requirements
Regional Considerations for Kansas City Businesses
Climate-Specific Optimization
Kansas City's diverse climate demands adaptive HVAC strategies:
Summer Efficiency Strategies
- Advanced cooling techniques
- Humidity control mechanisms
- Heat load management
- Thermal storage solutions
Winter Performance Enhancements
- Efficient heating system configurations
- Minimal heat loss technologies
- Insulation optimization
- Strategic ventilation management
Economic Incentives and Benefits
Cost Savings Potential
- Potential energy cost reduction of 20-40%
- Rapid return on technology investment
- Increased property value
- Enhanced operational efficiency
Available Incentive Programs
- Local utility rebates
- Federal energy efficiency tax credits
- Missouri state energy conservation programs
- Commercial energy efficiency grants
Service Areas We Proudly Serve
Anderson Mechanical provides cutting-edge HVAC solutions across:
- Kansas City, MO
- Kansas City, KS
- Overland Park
- Olathe
- Shawnee
- Lenexa
- Prairie Village
- Johnson County
- Wyandotte County
- Jackson County
Conclusion: A Smarter Approach to Commercial HVAC
Energy efficiency is no longer just an option—it's a competitive necessity. By leveraging smart HVAC technologies, businesses can significantly reduce operational costs, enhance workplace comfort, and demonstrate environmental responsibility.
Ready to transform your commercial HVAC system?
Contact Anderson Mechanical
for a comprehensive energy efficiency consultation tailored to your specific business needs.
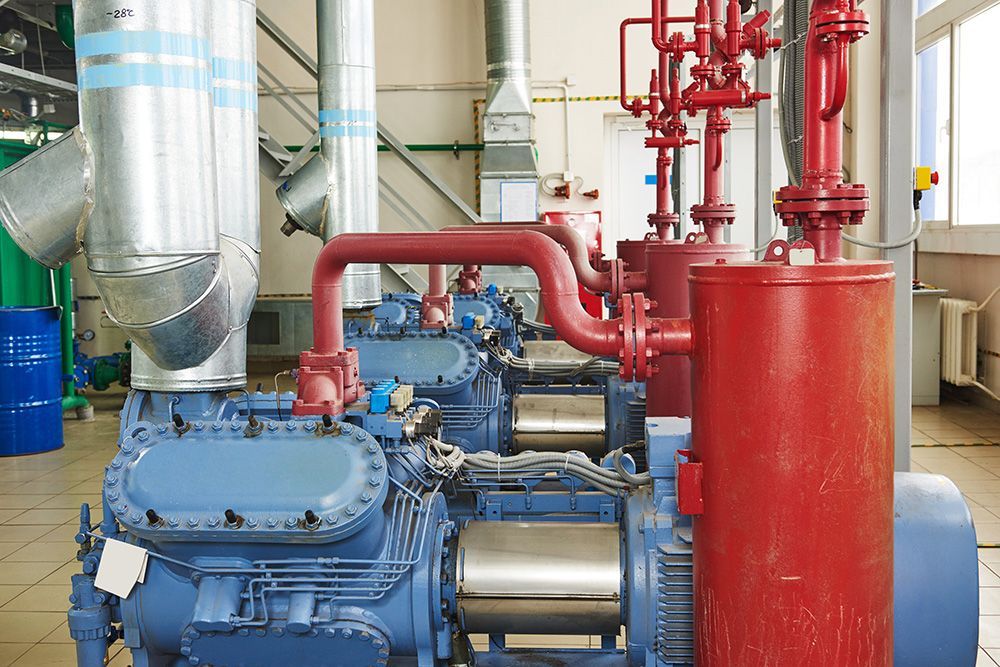
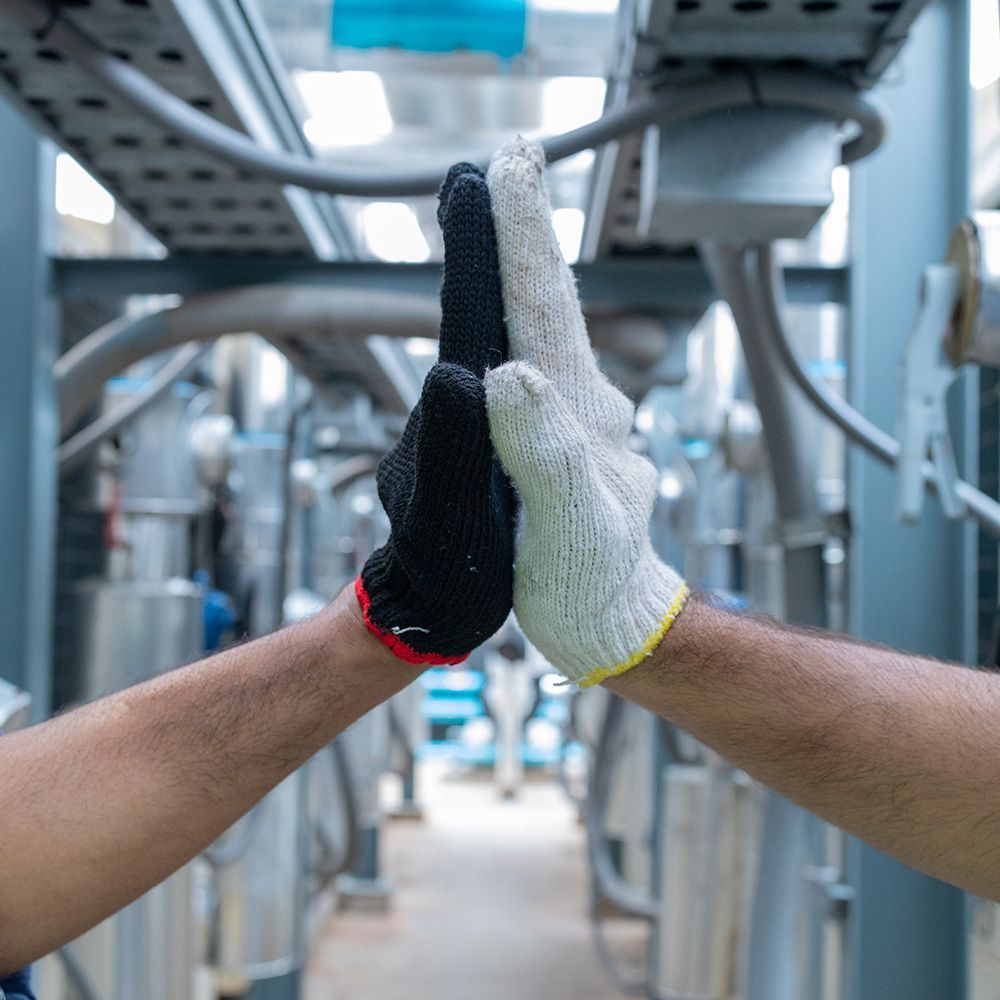
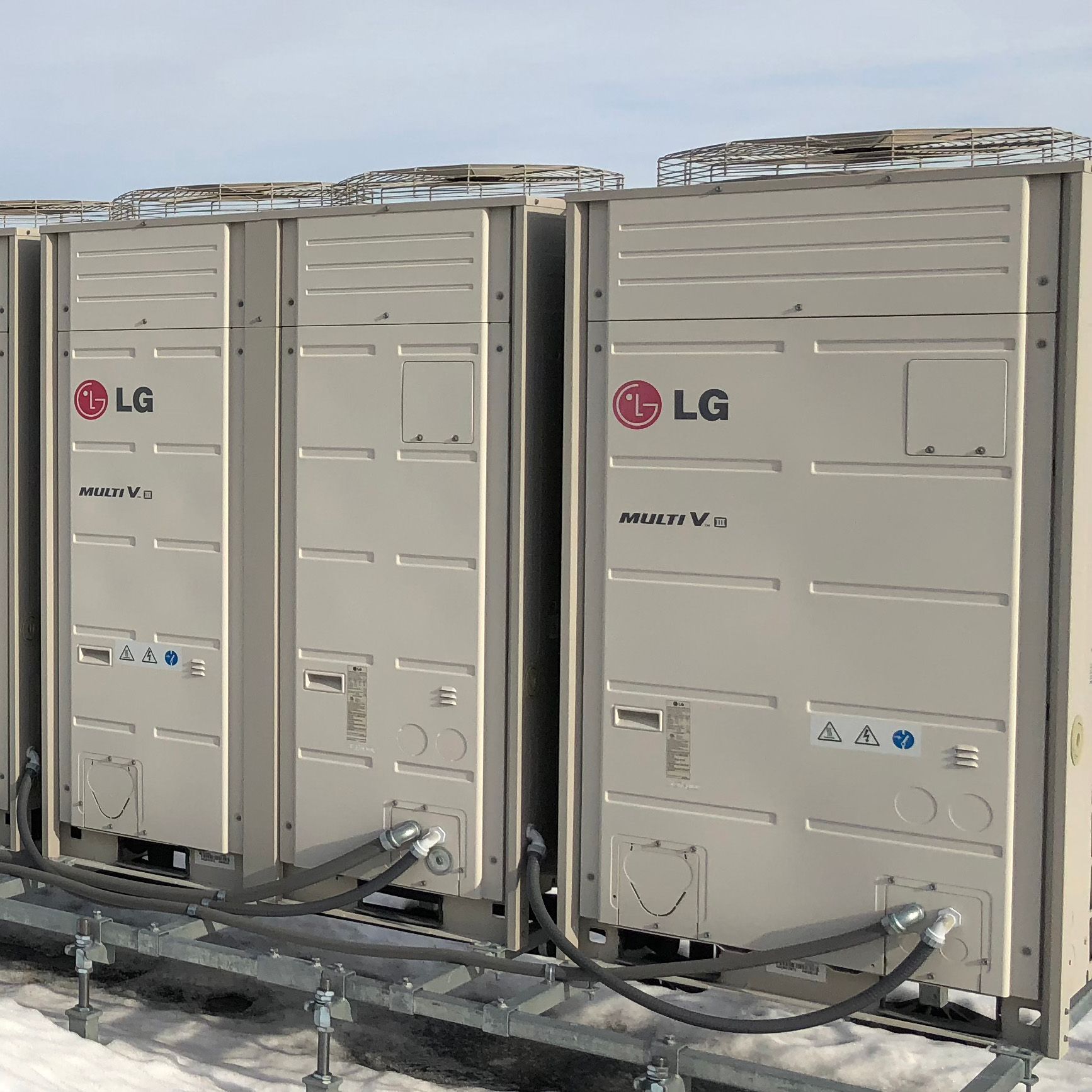